Here's some chemistry history to think about next time you do your laundry.
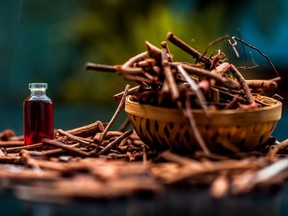
What an odd term: “Turkey red oil.” It has nothing to do with fowl. It owes its name to a connection with the dye known as “Turkey red,” which in turn is named after the country of Turkey from where it was first imported into Europe around the 18th century. The source of the dye is the root of the madder plant, Rubia tinctorum, which was cultivated in China, India and Egypt long before Turkey existed as a country. Cloth dyed with madder was recovered by archeologists exploring the ancient city of Mohenjo-daro, founded around 2500 BC, now in Pakistan, and was also found in the tomb of Tutankhamun.
Various methods of producing cloth dyed red with madder have been handed down through history, with a host of curious steps involved. It starts with steeping the fabric in rancid olive oil, soda ash and sheep dung, then treating it with alum, and finally dyeing in vats of madder extract and bullock’s blood. Exactly which of these ingredients were critical was contentious, but the olive oil and soda ash were likely functional because they react to produce soap. When it comes to dyeing, it is important that fabrics contain no greasy residues that prevent the dye from adhering.
Sign up to receive daily headline news from the Montreal Gazette, a division of Postmedia Network Inc.
Thanks for signing up!
A welcome email is on its way. If you don't see it, please check your junk folder.
The next issue of Montreal Gazette Headline News will soon be in your inbox.
A major step forward was taken in 1831, when French chemist Edmond Frémy reacted olive oil with sulphuric acid. Upon neutralizing the solution with lye, he obtained a liquid with a soapy feel that lathered when mixed with water. He didn’t realize it, but he had actually made the world’s first synthetic detergent. Unlike soap, it did not react with calcium or magnesium in water to produce an insoluble scum that was the bane of dyers.
This sulphated olive oil turned out to be adept at removing grease from cloth and, as is often the case with science, spurred efforts to find “new and improved” versions. Various animal fats and plant oils were reacted with sulphuric acid with the oil extracted from castor beans proving to be especially useful. Sulphated castor oil was great for treating cloth prior to dyeing, particularly with Turkey red. It was christened “Turkey red oil” and was embraced by European dyers. But their joy didn’t last very long.
In 1869, German chemists Carl Graebe and Carl Liebermann, working for the chemical company BASF, and English chemist William Henry Perkin independently found a way to synthesize alizarin, the red component of madder root, from anthracene extracted from coal tar. This made Turkey red the first natural dye to be duplicated synthetically. As a result, the madder industry, estimated to be worth about $16 million a year, an astounding amount at the time, collapsed almost overnight. Synthetic alizarin was cheaper and easier to use. But eventually, it, too, was replaced by more light-resistant quinacridone pigments developed by DuPont in 1958.
The downfall of the madder industry did not spell the end for Turkey red oil since it was still effective for treating cloth before dying with synthetic alizarin. Today, it is used as a dyeing assistant, an emulsifier in cosmetics, and in aromatherapy products where dispersion of essential oils in water is important. But what is of greater interest, is the role Turkey red oil was destined to play in the creation of the modern detergent industry, although in a round-about way.
Until the 1930s, laundry products were based on soap. Companies such as Procter & Gamble, Lever Brothers and Colgate-Palmolive were major producers but were saddled with a problem. Soap worked well in “soft” water with a low mineral content, but in “hard” water it reacted with calcium and magnesium to produce a precipitate that would deposit on clothes. How to solve this problem? A clue began to emerge in Germany during the First World War when fats to make soap were in short supply because they were needed to produce lubricants and glycerol for nitroglycerine. Alternatives for cleaning were needed, and the I.G. Farben Company turned to ox bile, since this fluid, produced in the liver, was known to aid digestion by breaking down fats, much like soap. Bile didn’t turn out to be a very good cleaning agent, but it did prove to be useful in the textile industry as a “wetting agent,” allowing a dye solution to penetrate fabrics.
Given the size of the textile industry, Igepon, as the product was marketed, stirred up competition. The Deutsche Hydrierwerke Company, aiming for an “improved” version, now harkened back to Turkey red oil. Like Igepon, it was not a great cleaner, but was also unaffected by hard water. Instead of using ricinoleic acid from castor oil, the company’s chemists turned to reacting lauric acid from palm kernel or coconut oil with sulphuric acid. Indeed, the sodium lauryl sulphate produced turned out to be excellent agent for treating textiles before dyeing and was not bothered by hard water. The company, however, never thought of using it as a detergent for home use because it was not in the laundry product business.
As luck would have it, Robert Duncan, a process engineer with Procter & Gamble, was visiting German chemical plants in 1931 to see if they were involved in any research potentially useful for his company. He heard about the sodium lauryl sulphate (SLS) story and was intrigued by the substance’s immunity to hard water given that scum was a major problem with P&Gs soap products. He purchased 100 kg and had it shipped back to Cincinnati.
Within a couple of years, P&G chemists confirmed that SLS worked well in hard water and Dreft, the first commercial synthetic laundry detergent, appeared on the market. It was only moderately successful because it did not work well on heavily soiled clothes. Clearly “new and improved” versions were needed. Dogged work by chemist David Byerly, code -named “project X,” resulted in greatly improved cleaning efficiency with the addition of sodium tripolyphosphate, and Tide was born. Many improvements in the formulation have been made since then, but it is interesting to note that it was Turkey red oil that turned the tide when it came to the introduction of the synthetic detergents we drop in our washing machines without much thought as to their origin.
joe.schwarcz@mcgill.ca
Joe Schwarcz is director of McGill University’s Office for Science & Society (mcgill.ca/oss). He hosts The Dr. Joe Show on CJAD Radio 800 AM every Sunday from 3 to 4 p.m.
-
The Right Chemistry: Reflections on the manufacture of mirrors
-
The Right Chemistry: The history of Tylenol
-
The Right Chemistry: Soap-making, from early Europe to the Beverly Hillbillies